Industrial Robot Controller C1102
Product Introduction
The iNexBot C1102 EtherCAT industrial robot control system adopts IPC+RTOS design. It supports X86 and ARM computing platforms, as well as various real-time operating systems.
iNexBot's self-developed control algorithms can support standard robot configurations such as serial multi-joint, parallel multi-joint, SCARA, Cartesian, and linkage structure. It also offers customization options for developing specialized multi-joint robots with specific structures.
Because of iNexBot's excellent hardware platform and algorithm capabilities, the NRC series control system can support heterogeneous multi-robot collaboration, synchronous motion of up to 64 axes, and interpolation calculations.
Currently, iNexBot has a wide range of general processes such as arc welding, argon arc welding, laser welding, resistance welding (spot welding), laser cutting, spraying, dispensing, palletizing, and conveyor tracking. Additionally, iNexBot can also provide customized process development according to user requirements to meet specific application needs.
With the NexDroid OpenAPI interface, users can also design and develop their own process systems and human-machine interaction interfaces, and even implement dedicated robot forward and inverse kinematics and trajectory planning algorithms.
The iNexBot control system has been verified on tens of thousands of industrial robot equipments, and its reliability and stability are worthy of customers' trust. Besides, iNexBot's unique NexDroid OpenAPI provides high scalability and configurability to meet the needs of customers in different fields.
Product Features
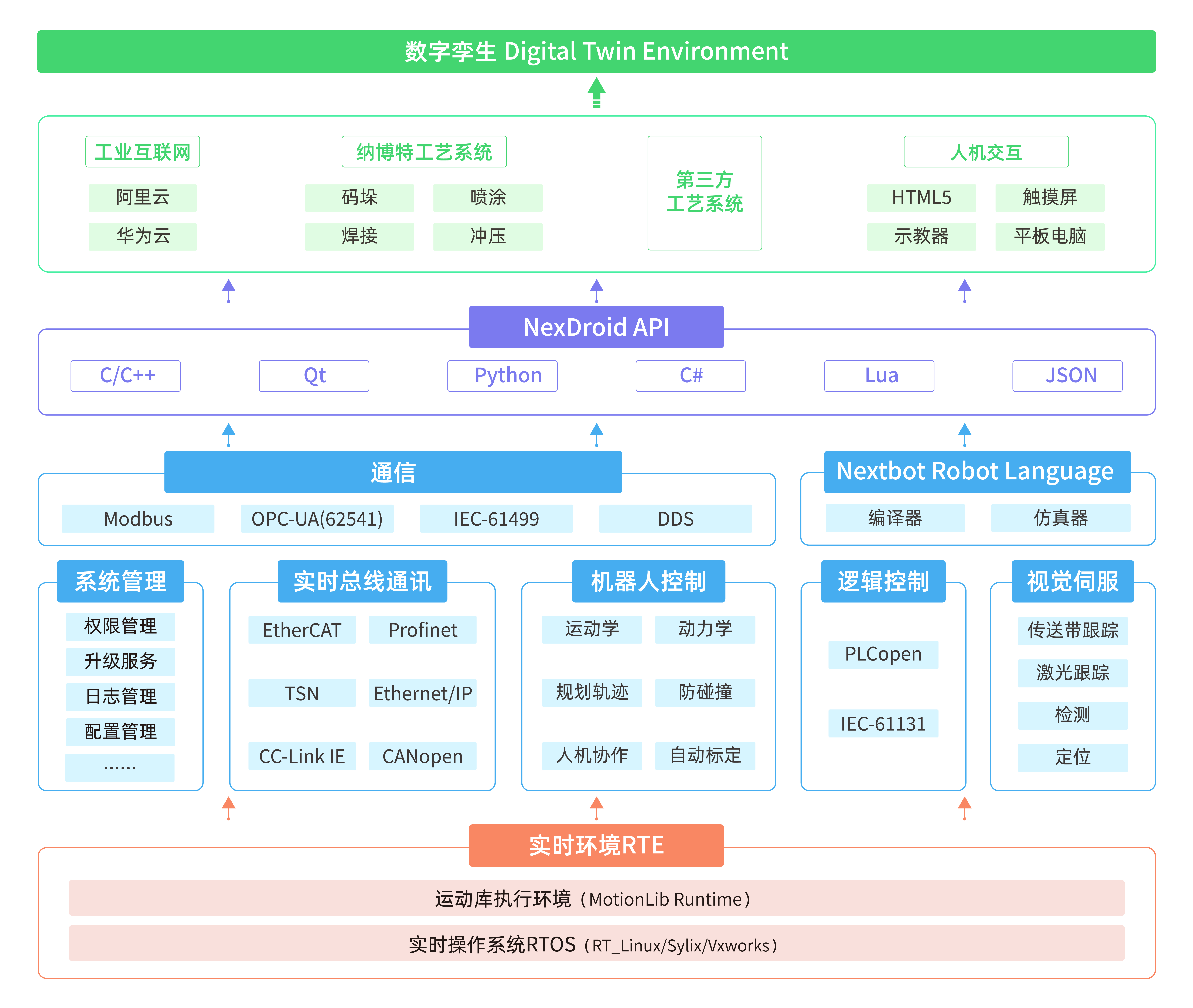
Good scalability. The NRC series robot controller adopts EtherCAT and PowerLink buses to realize servo master-slave connection, supporting synchronous motion of up to 64 axes. It is widely used in the control of robots and CNC equipment. Compared to the traditional pulse-controlled solutions, it significantly reduces system wiring and maintenance costs, and has excellent scalability.
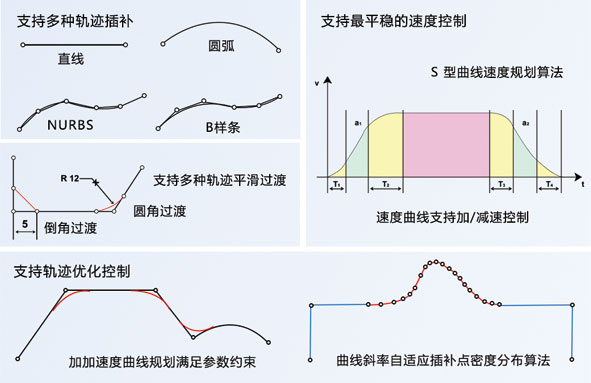
Supports multi-robot collaboration and secondary development. The NRC supports multi-robot collaboration, enabling simultaneous control of 4 industrial robots, and supports customer's secondary development.
Product Parameters
Model | C1102 |
---|---|
CPU | Intel Celeron J1900 2.0GHz |
RAM | 2G |
Power supply | 24V (±10%) |
System | Linux RT |
Network port | 1*EtherCAT, 1*EtherNet |
USB | 1*USB 3.0, 3*USB 2.0 |
COM | 1*RS232, 1*RS485 |
Teach pendant | (Optional) T30 dedicated teach pendant for robots: 8-inch TFT touchscreen, Linux+QT |
Control axes | 64-axis simultaneous interpolation motion / 6-axis serial robot + ground rail + 2-axis positioner*2 |
Communication protocols | EtherCAT, Profinet, Profibus, Ethernet/IP, CAN, CC-Link IE TSN, OPC-UA, FinsTCP, FinsUDP, TCP/IP, ModbusTCP, ModbusRTU |
Operation mode | Teach, Auto, Remote |
Programming method | Teach programming, Offline programming, Drag teaching |
Motion function | Point-to-point, straight line, circular arc, spline curve, linear swing, FLYBY |
Instruction system | Motion instruction, logic instruction, input/output instruction, operation instruction |
Position control method | Point-to-point control, continuous trajectory control |
Coordinate system | Joint coordinate system, Cartesian coordinate system, tool coordinate system, user coordinate system |
Structure algorithms | More than 20 configurations, including 6-axis serial robots More details |
Applications | Arc welding, argon arc welding, laser welding, resistance welding (electric welding), stamping, loading and unloading, laser cutting, spraying, dispensing, palletizing, conveyor tracking, etc. |
Dimensional diagram

Advantages
Real multi-robot
Supports controlling up to 4 robots simultaneously with one controller, where each robot has independent parameters and programs. In run and remote modes, all robots can be synchronized to start and stop together. It supports a one-to-many configuration, allowing each robot to be paired with any type of external axis, such as a ground rail, positioner, or gantry system. Furthermore, the system also supports dual-robot collaboration mode, enabling two robots to start and stop in complete synchronization.
Built-in general processes
The system is equipped with various general processes such as loading and unloading, palletizing, welding, weld seam tracking, vision, laser cutting, conveyor tracking, collision detection, and drag teaching, and can be customized according to user needs. By utilizing the built-in general process functions, users can easily and quickly implement the desired process.
Open interfaces
iNexBot open platform NexDroid provides open API interfaces, allowing everyone to develop applications. It supports customers to perform secondary development and integrate processes based on C/C++/Python/Lua, enabling them to have control over core process experience. This is beneficial for protecting customers' intellectual property and domain expertise.
Offline programming
The iNexBot control system supports offline programming techniques and is now compatible with multiple offline programming vendors, including SprutCAM, RobotMaster, and RobotDK. It can be widely used in various fields such as engraving and spraying.
High precision
With the support of robot body accuracy, the NRC series control system can achieve a trajectory accuracy of within ±0.4mm and a repeat positioning accuracy of within ±0.02mm.
Flexible programming
In addition to traditional teach pendant programming, we also provide PC-based teaching software and configuration software-based touchscreen programming modes.